
Find your nearest LINE-X Store.
View Service Information for Protective Coatings
Read more Articles on Protective Coatings
Steel, iron, and other materials usually require an enhanced barrier to protect them from corrosion, improve wear resistance, and extend their life span. This protective layer is particularly important in industries that make use of expensive equipment and machinery, such as in construction, manufacturing, shipping, agriculture, and oil and gas.
You can also change the way your car, bike, or truck looks like by merely applying a layer of paint or some other type of protective coating. While paint can and does offer some protection, its applications are limited.
There are other coating options more durable than paint, such as LINE-X protective coatings, thermal spray, and epoxy.
An alternative to protective coatings is powder coating, which produces a more durable barrier than paint and certain types of protective coatings. However, it has some limitations in terms of application.
To give you a more comprehensive understanding of the different coating methods below is some information on powder coating and common protective coatings.
Powder Coating Options
Unlike paint, powder coating makes use of dry, free-flowing powder – made of thermoplastic or another type of thermoset polymer – delivered electrostatically. This electric charge ensures the powder adheres to the surface.
The metal is then baked or cured under heat or ultraviolet light, turning the powder into a durable, solid protective coat.
Aside from its durability, powder coating releases negligible amounts of volatile organic compounds or VOCs, unlike paints. It also cures a lot faster than paint due to the baking method used.
Powder coating is, however, quite expensive, and facilities that provide powder coating services have size limits. There are also set prices for small and larger parts to be powder coated.
- Versatility: Can be used on virtually all metals.
- Durability: Depending on the pre-treatment material and type of powder, powder coating can maintain its finish for 15 to 20 years.
- Value for Money: Generally expensive to apply initially and repair when it starts to chip.
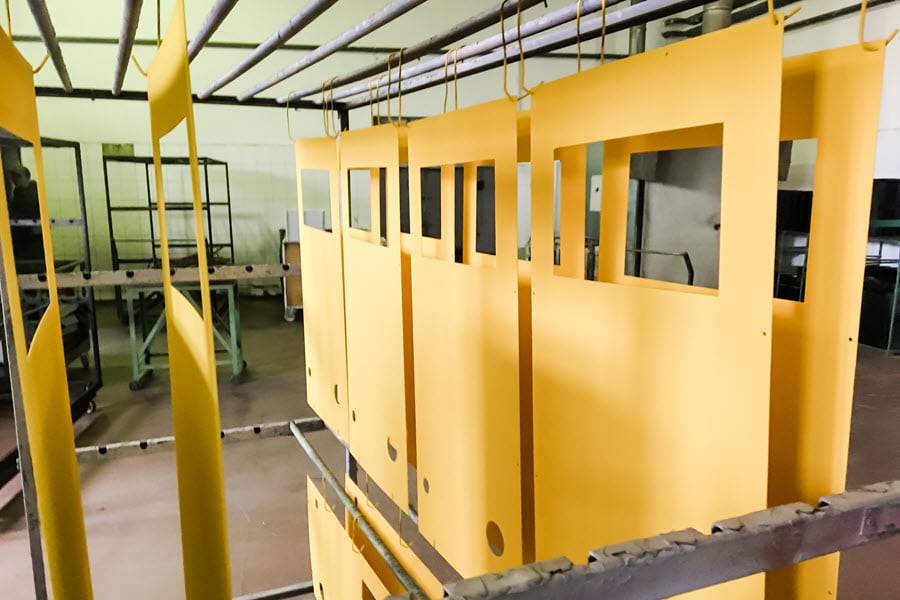
Protective Coatings vs Powder Coatings
Here’s a rundown on some of the most common types of protective coatings:
1. LINE-X Protective Polyurea Coatings
LINE-X protective coatings are spray-on protective coatings made from polyurea. They are extremely durable and resistant to impact, heat, chemicals, and corrosion.
The protective coating can be applied to almost anything, including mining and industrial machinery, agricultural farm equipment, commercial construction equipment, boats, trailers, and even bridges.
LINE-X protective coatings come with custom colour pigmentation and have excellent adhesion to different surfaces like metal, concrete, fibreglass, plastic, and wood. Some LINE-X coatings are also rated for fire safety and approved for use in potable water applications.
- Versatility: Since LINE-X adheres to almost any substrate, it has a wide range of applications.
- Durability: LINE-X protective coatings permanently bonds to most materials at a molecular level, so the resulting composite has exceptionally high tensile strength. It is more durable than powder coating and other protective coating options.
- Value for Money: The durability and longevity of LINE-X protective coatings ensure the need for minimal ongoing costs – making the lifetime cost of the product very attractive.
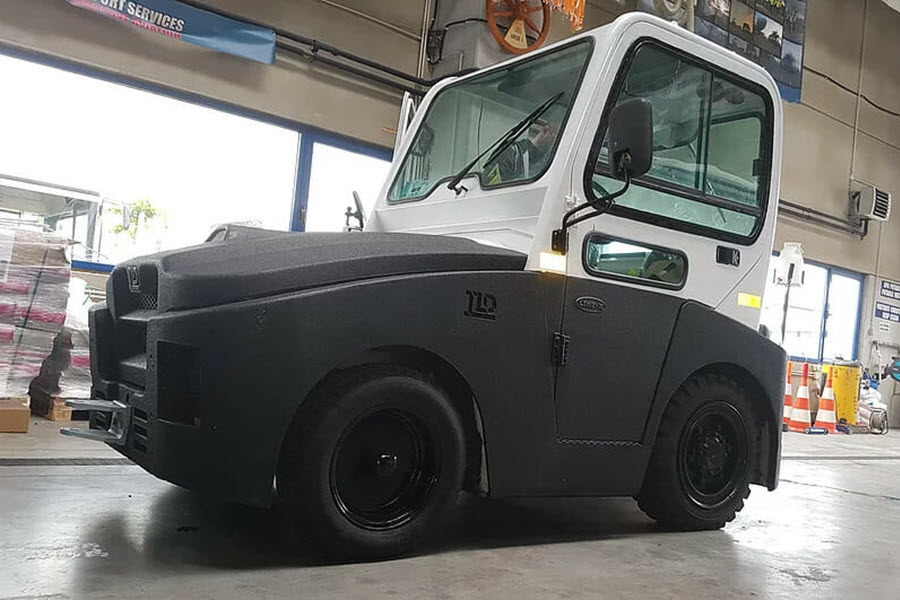
2. Industrial Painting
Industrial painting is probably the most accessible and cheapest type of protective coating.
It is extensively used in the automotive industry since it can be applied to all exterior components, including body panels, bumpers, wheels, etc. If it chips, it is fairly easy to touch up.
All materials required to use it can be easily purchased as well, including the paint, brushes, and cleaning supplies. However, all paints contain VOCs.
- Versatility: Suitable for certain smaller industrial applications on metal and plastics.
- Durability: Not durable enough to be suitable for some industries that require tougher, longer-lasting material protection.
- Value for Money: While paint is relatively cheap, there are better, more durable alternatives for industrial applications.
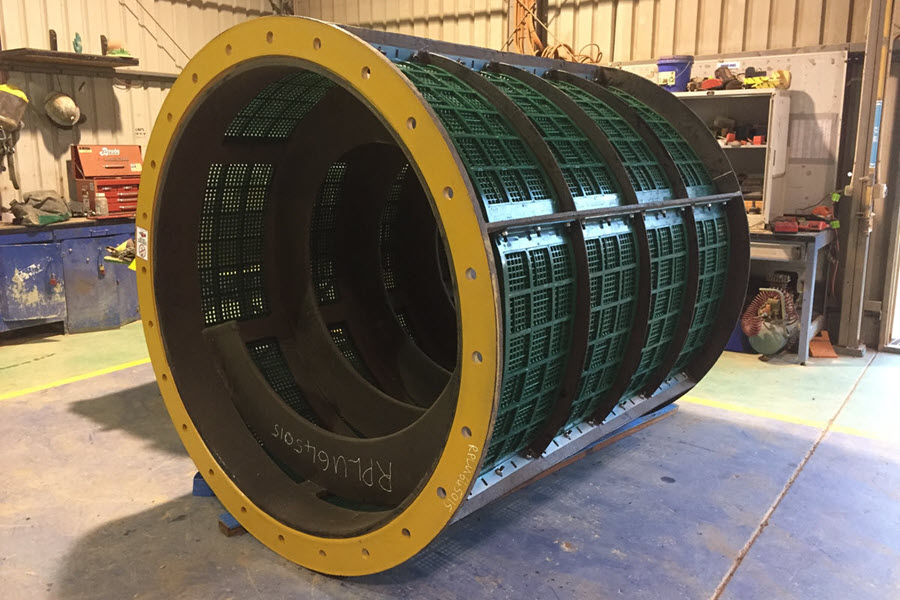
3. Thermal Spray Coating
Thermal spraying uses a heat source and a high-pressure applicator designed for applying a specific coating material – whether it is a metal, alloy, plastic, composite, or ceramic. The heated or melted coating material is sprayed onto the surface that requires protection.
Aside from providing corrosion protection, thermal spray coating works great for repairing damaged surfaces, wear control, and oxidation/temperature protection. It is also known to be VOC-free.
However, since this process requires specialised tools, you need to find a facility that provides this service.
- Versatility: Both metals and flammable substances like plastics can be coated in this manner.
- Durability: Compared to powder coating, thermal spray coatings can last for as long as 30 years.
- Value for Money: The upfront costs tend to be higher for thermal spray coating; however, its durability makes the initial investment more attractive.
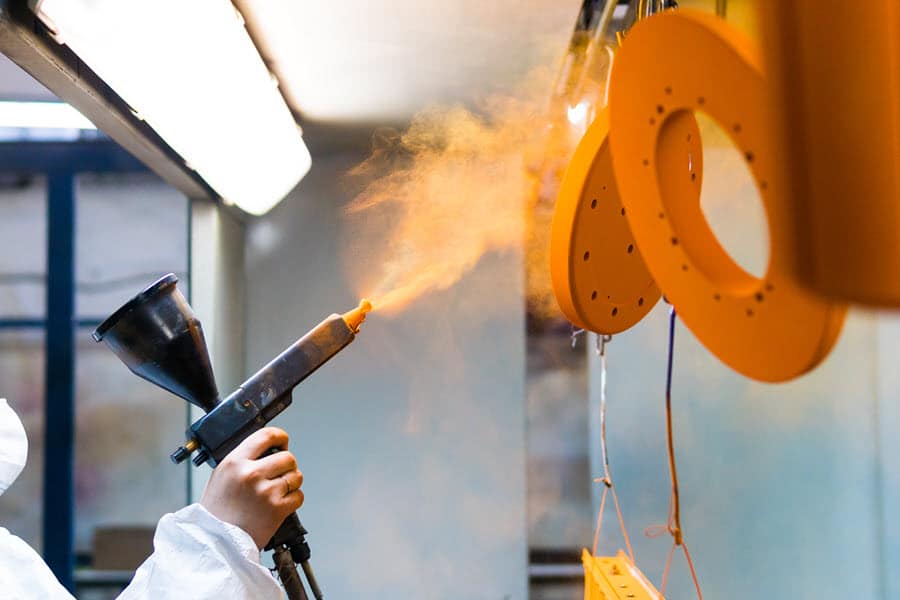
4. Epoxy Coatings
An epoxy coating is composed of an epoxy base and finish coat or curing agent. Different components of epoxy can be manipulated to provide certain benefits.
For example, epoxy polyamide coatings provide superior moisture resistance, phenolic epoxy coatings provide excellent chemical resistance, and epoxy mastic coatings ensure exceptional film thickness.
The versatility of epoxy means you’ll find them across a wide variety of industrial settings, such as nuclear power plants, construction, agriculture, oil and gas, and wastewater treatment facilities. It performs well even underwater and is abrasion-, heat-, and chemical-resistant. It is also generally affordable.
However, UV exposure leads to the deterioration or chalking of epoxy.
Epoxy is commonly used when applying a protective coating to industrial and workshop floors, although there are more durable alternatives to epoxy coatings.
- Versatility: Epoxy can be used on metal surfaces, PVC, glass, ceramic tiles, fibreglass, wood, concrete, etc.
- Durability: Epoxy provides moderate durability, however more advanced polyurea coatings usually provide more advanced protection.
- Value for Money: Epoxy is often superior to powder coating in terms of price and durability.
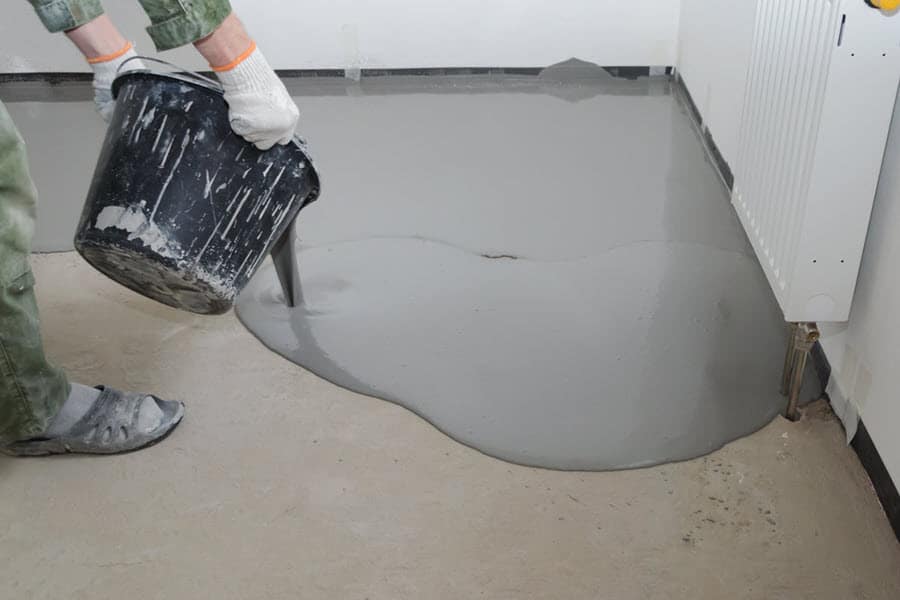
The Benefits of LINE-X Protective Coatings
LINE-X protective coatings provide an impenetrable layer of polyurea designed to shield your valuable equipment and vehicles from the elements, including humidity, saltwater, and extreme temperatures.
It is heat-, corrosion-, and chemical-resistant has no VOCs, and is extremely durable, with tensile strengths of up to 6,600 psi. It has fast cure times and is also UV- and colour-stable.
LINE-X is guaranteed to weather the harshest environmental conditions, which is why it is extensively used in industrial, commercial, agricultural, municipal, and recreational settings.
Not only do LINE-X protective coatings our perform all other protective coatings on the market, but it is also more durable than powder coating and can be used for a wider range of applications.
We also produce spray-on ute tray protection with LINE-X automotive coatings.
If you require a durable, high-performance coating for your materials, vehicles and equipment, get in touch with one of our many Australian locations.